穿透硅基的“智慧之眼”:近红外成像重塑半导体检测新维度
在半导体器件持续微缩与三维堆叠技术爆发的今天,传统检测手段已难以满足高密度封装内部的无损检测需求。近红外成像技术(NIR)凭借其独特的**硅材料穿透能力**和**亚微米级分辨率**,正成为电子设备与半导体检测领域的“透视眼”。作为深耕光学影像领域二十年的领军者,上海温网数码科技有限公司以“看得清,看得见,看得远”为核心理念,将前沿近红外成像技术与工业应用深度融合,为半导体制造注入全新动能。
一、技术基石:近红外成像的穿透原理与核心装备
近红外成像的核心优势源于硅材料的光学特性。单晶硅的带隙对应1100nm光子能量,**波长大于1100nm的光可穿透硅基材料**,最高穿透厚度达700μm,而可见光则被完全阻挡。这一特性使其能够**无损捕捉芯片内部结构**,避免X射线的电离辐射风险或超声波检测所需的水耦合剂。
整合的国际领先成像系统包含三大核心组件:
- **透射光显微镜系统**:如MX63红外显微镜,通过底部透射照明提升对比度,专用于集成电路内部缺陷检测;
- **高灵敏度相机**:采用制冷型InGaAs传感器(响应波段900-1700nm)或近红外增强型CMOS相机(如640万像素DP23M),搭配1100nm带通滤光片,实现硅内部微米级线路成像;
- **专用红外物镜**:LCPLN-IR系列物镜配备厚度校正环,可针对不同硅层厚度优化像差,支撑20×至100×多尺度观测。
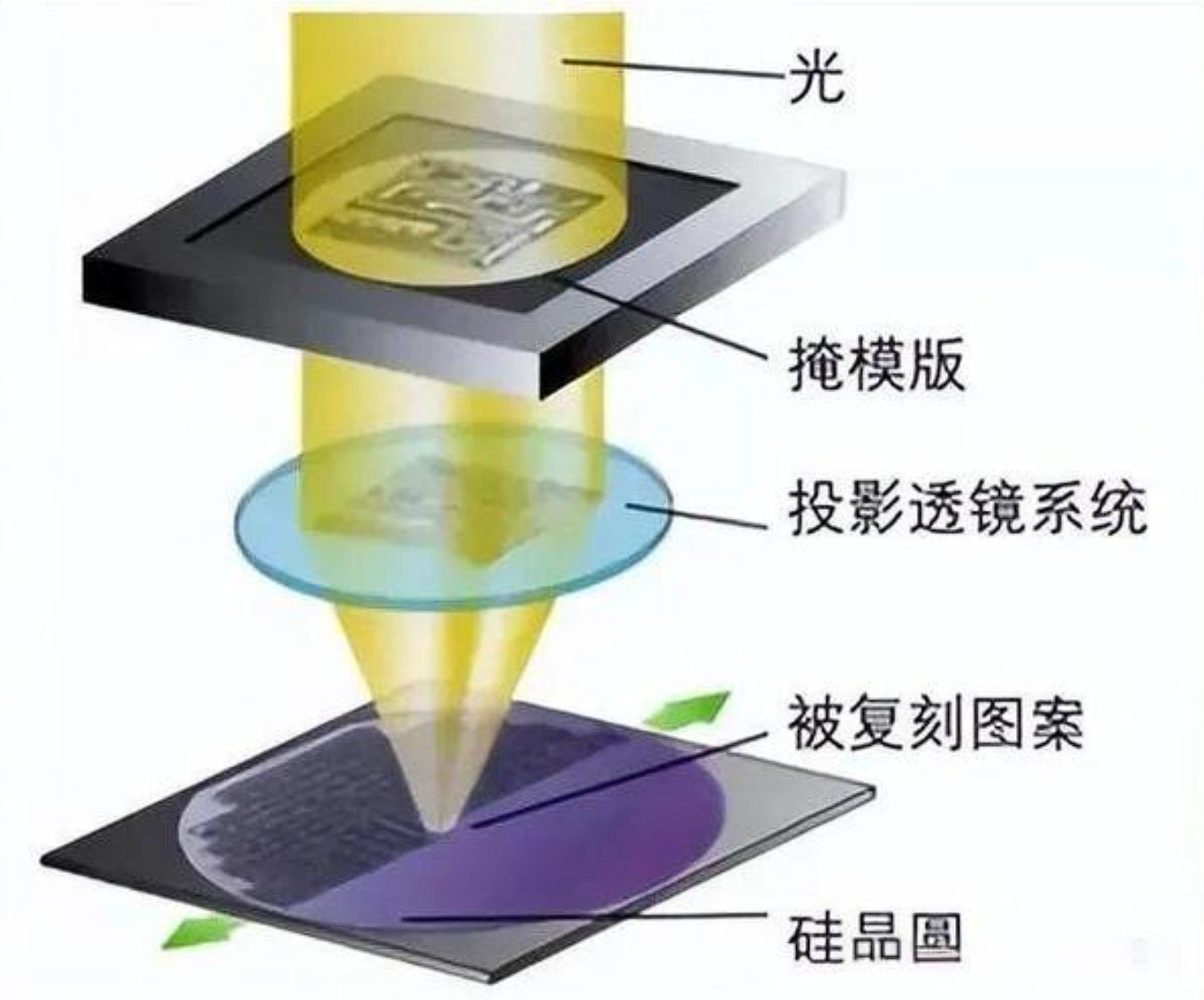
二、工业场景:半导体检测的五大应用突破
1. 倒装芯片与键合结构无损分析
在手机处理器等倒装芯片封装中,焊点隐藏于芯片下方。近红外光可穿透硅基体,直接观测**焊点空洞**或**标记点错位**。例如苏州卡斯图MIR400系统可实现3D堆叠芯片的逐层检测,替代传统破坏性切片。
2. 晶圆级封装(WLP)缺陷筛查
在晶圆研磨工艺中,通过物镜Z轴移动量测,红外显微镜可**无损判定研磨厚度**,精度达微米级。同时可检测热湿测试后的熔炼泄漏、铜线腐蚀等失效。
3. 光电器件电致发光(EL)检测
光电子芯片在低电流激发下发射近红外光。InGaAs相机捕捉发光形貌,可识别**激光巴条断点**、**多晶硅裂痕**等缺陷,避免器件早期失效。
4. 3D IC与硅通孔(TSV)质检
针对2.5D/3D封装中的TSV结构,近红外成像可清晰呈现**金属互连层导通状态**。某封测企业采用温网数码合作的MIR200系统后,TSV检测效率提升40%,复检工作量减少70%。
5. 光通信器件耦合优化
1550nm/1310nm通信激光的光斑形态直接影响耦合效率。通过InGaAs相机分析输出光斑,可量化**光纤-波导对准偏差**与**传输损耗**。
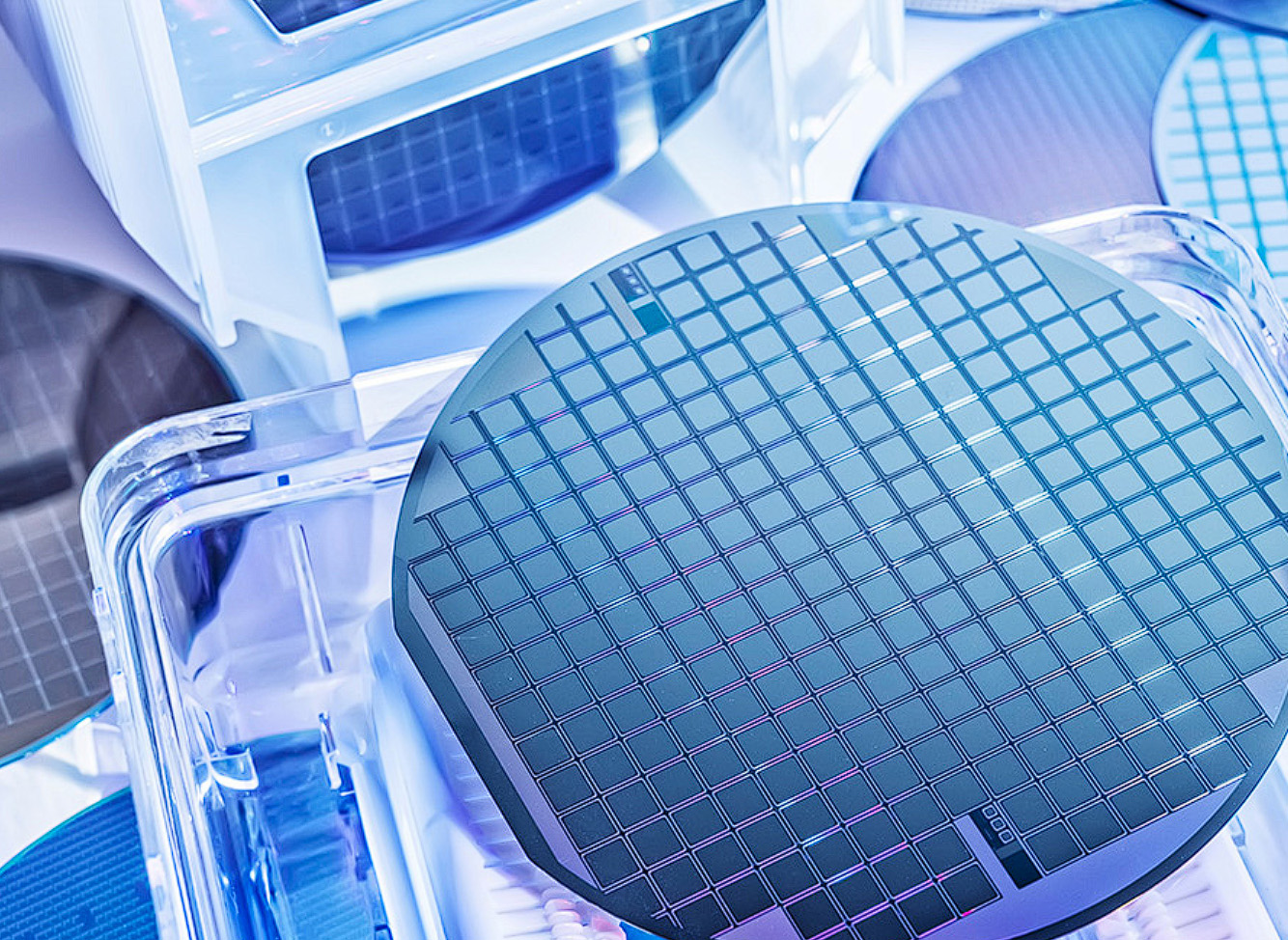
三、技术对决:近红外 vs. X-ray vs. 超声扫描
常基于客户需求推荐三者的协同策略。以下是核心参数对比:
检测技术 | 近红外显微镜 | X-ray检测 | 超声显微镜(SAM) |
分辨率 | 0.5-1 μm | 0.05-1 μm | 5-50 μm |
穿透材料 | 硅/树脂等非金属 | 全材料 | 多层复合材料 |
检测速度 | 实时动态观测 | CT扫描耗时 | 逐点扫描慢 |
典型缺陷检出 | 键合线断裂、TSV缺陷 | 焊球裂纹、BGA空洞 | 界面分层、脱粘 |
单机成本 | 中等(100-300万元) | 超高(超千万元) | 中高(200-500万元) |
四、创新实践
1. **智能光学适配**:电动物镜塔轮支持5×-100×镜头自动切换,适配从薄晶圆到塑封器件的全厚度检测;
2. **AI缺陷分析引擎**:集成深度学习算法,可自动标记键合线断裂、树脂空洞等缺陷,误检率<1%;
3. **多模态数据融合**:支持与电性测试仪、热成像仪联机,构建“结构-功能”关联分析平台。
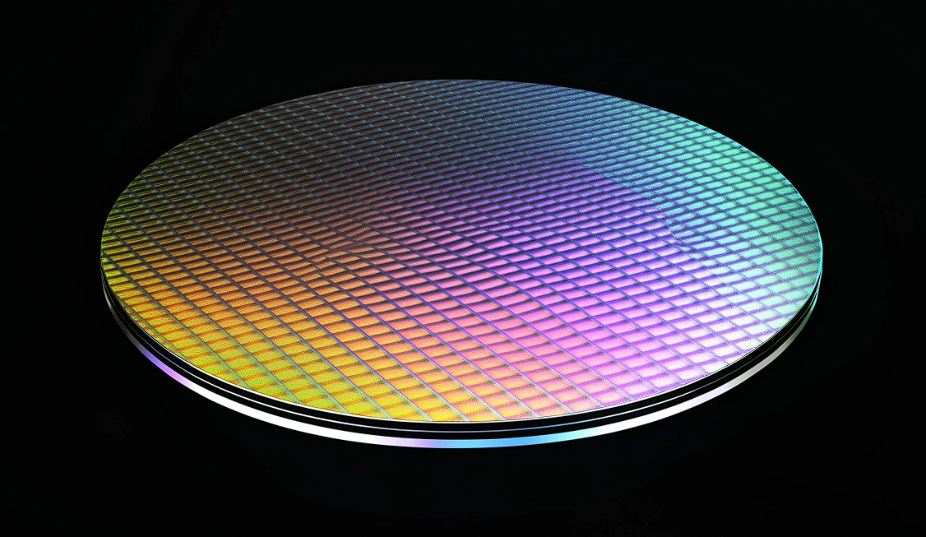
五、未来趋势:多模态融合与超分辨突破
随着Chiplet和3D IC技术普及,近红外成像正向三个维度进化:
- **分辨率极限突破**:结合STED超分辨技术,目标突破衍射极限至100nm级别;
- **多光谱层析**:卡斯图下一代MIR系列将集成太赫兹波模块,拓展对陶瓷、复合材料的穿透;
- **高速动态捕捉**:毫秒级成像能力可实时观测芯片工作时的电流分布与热点形成。
从晶圆表面的电致发光分析到3D封装的内部透视,近红外成像以**无损、高效、高分辨**的特性,成为半导体工业不可或缺的“智慧之眼”。上海温网数码作为该技术的整合者与推广者,正通过持续创新的光学方案,推动中国半导体检测迈向“穿透一切硅障”的新纪元。当芯片堆叠如摩天大楼般高耸入云,唯有近红外这双“眼睛”,能让我们看清每一层“楼板”的坚实与否,守护算力时代的根基。